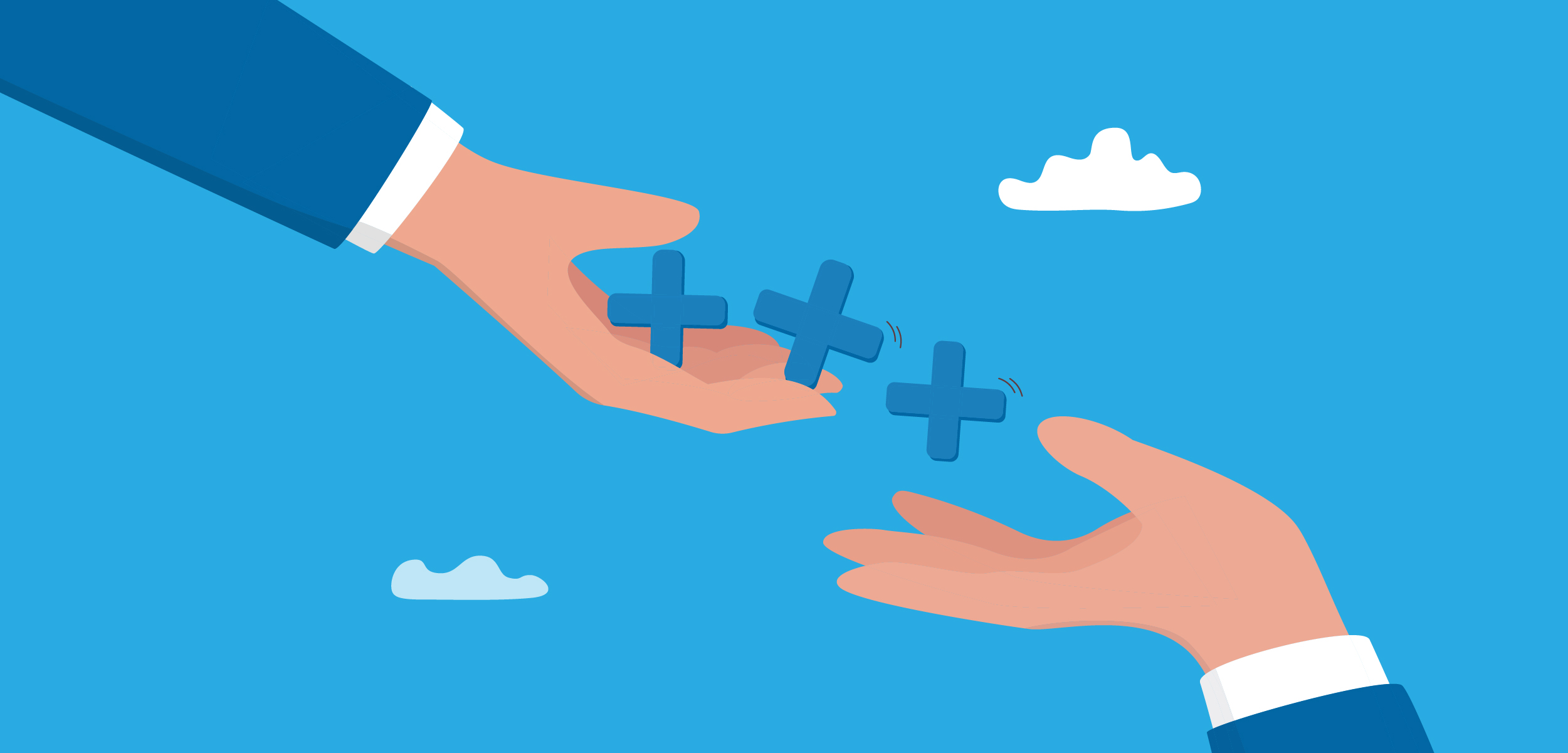
Participaciones
Centro de Investigación de Ingeniería de Materiales y Procesos
Casi la mitad de los profesores del Departamento de Ingeniería Mecánica y de Plásticos trabajan en el Centro de Investigación de Ingeniería de Materiales y Procesos ( fz mpt ). El objetivo es aumentar la eficacia de los procesos y desarrollar nuevos tipos de procesos. Mediante la comprensión de la dependencia de las propiedades de los productos del proceso de fabricación y la consiguiente capacidad de predecir propiedades utilizando métodos de simulación, se puede aumentar el potencial de los materiales y las materias primas en términos de eficiencia en aplicaciones posteriores. Parecen tareas apasionantes y desafiantes.
Centro de Doctorado en Ciencias de la Sostenibilidad
Ahora hay aún más motivos para que todos los jóvenes científicos estén contentos: ¡puedes hacer un doctorado! En el Centro de Doctorado en Ciencias de la Sostenibilidad tienes la oportunidad de obtener el título académico de Doctor en Ciencias de la Sostenibilidad (Dr. rer. sust.). Este título, único en Alemania, fue creado específicamente para el centro de doctorado e integra varias ramas de la ciencia y la investigación con el fin de obtener conocimientos sobre los retos sociales, socioeconómicos, de ingeniería (o técnicos) y científicos. Un requisito fundamental es no ver los problemas individuales desde perspectivas disciplinarias separadas. ¿Inspirador? ¿A qué espera? Déjese inspirar por el impulso del Centro de Doctorado en Ciencias de la Sostenibilidad .
Doctorados cooperativos con la TU de Berlín
Procesado y caracterización de mezclas de poliamida 6 y polihidroxibutirato
Svenja Dill
Debido a los rangos de procesamiento significativamente diferentes del polihidroxibutirato (PHB) y la poliamida 6 (PA 6), el procesamiento conjunto de ambos polímeros supone un reto en términos de ingeniería de procesos. Para evaluar la compatibilidad y procesabilidad de las mezclas PA 6-PHB, se desarrolló primero un proceso de preparación adecuado en una extrusora de doble husillo. Además, se llevó a cabo la producción de PHB coloreado (C) como compatibilizador. Utilizando mezclas de dos y tres componentes, se demostró que es posible producir las mezclas, pero que tienden a coalescer. Aunque los tipos C refinan parcialmente la morfología, no evitan eficazmente la coalescencia. Sin embargo, se puede demostrar un efecto compatibilizador limitado mediante microscopía de fuerza atómica e investigaciones mecánicas. También está claro que un efecto sinérgico de rigidización conduce a un aumento de los módulos de tracción de las mezclas. Como resultado, se alcanza hasta un 131% del valor de la PA 6 pura en el estado de secado por pulverización y un 151% tras el acondicionamiento. Mediante calorimetría diferencial dinámica y espectroscopia infrarroja por transformada de Fourier, el efecto podría atribuirse al aumento de la cristalinidad.
Comité de doctorado
Presidente: Prof. Dr. rer. nat. W. Reimers, Technische Universität Berlin Revisor: Prof. Dr.-Ing. D. W. Auhl, Technische Universität Berlin Revisor: Prof. Dr.-Ing. R. Weinlein, ikd, Darmstadt University of Applied Sciences
Día del debate científico: 17.12.2019, Universidad Técnica de Berlín
Enlaces:
Desarrollo del proceso de fabricación por capas fundidas para reducir la anisotropía del componente
Jens Butzke
Los procesos de fabricación generativa son una herramienta muy utilizada para la producción de prototipos en el entorno industrial desde hace más de 30 años. La fabricación por capas fundidas (FLM) genera muestras de visualización a partir de filamentos termoplásticos mediante el proceso de deposición de filamentos en 2½ dimensiones. El hecho de que este proceso sólo sea adecuado para la producción de muestras funcionales en una medida muy limitada se debe a la fuerte anisotropía de los componentes estratificados. El punto débil de los componentes con una mesoestructura es la adhesión de las capas individuales de los componentes entre sí. Las propiedades adhesivas reducidas en las costuras de unión se superponen además en las zonas de los bordes por las concentraciones de tensión introducidas continuamente.
Un sistema FLM de bajo coste, abierto tanto en términos de espacio como de software, con unos costes de inversión de unos 1.000 euros, se amplía para incluir la activación de superficies en línea. Esta ampliación, que cuesta menos de 250 euros, ha permitido mejorar notablemente la adherencia del revestimiento. Si una capa de un componente se activa con radiación infrarroja o aire caliente antes de aplicar la siguiente capa, aumentando así la temperatura en el momento de la unión, también aumenta la proporción cohesiva en la zona de unión. Estos entrelazamientos moleculares interlaminares deben desprenderse durante el ensayo de impacto destructivo según Charpy, que se caracteriza evidentemente por la formación de fracturas blancas. El aumento de la energía de impacto para destruir las probetas con superficie activada es representativo del aumento de la adherencia del revestimiento. Un análisis microscópico de la superficie de fractura muestra que la proporción cohesiva de la superficie total aumenta por la activación de la superficie.
La producción y el ensayo de las geometrías de las probetas investigadas en un sistema FLM de alta gama con un espacio de instalación cerrado templado a 75 °C y unos costes de inversión de unos 15.000 euros conducen a valores de adherencia del recubrimiento similares a los del sistema FLM de bajo coste y validan la funcionalidad del proceso desarrollado posteriormente.
Comité de doctorado
Presidente: Prof. Dr. rer. nat. W. Reimers, Technische Universität Berlin Revisor: Prof. Dr.-Ing. M. H. Wagner, Technische Universität Berlin Revisor: Prof. Dr.-Ing. R. Weinlein, ikd, Darmstadt University of Applied Sciences
Día del debate científico: 03.09.2018, Universidad Técnica de Berlín
Enlaces:
Disipación de la energía plástica durante el procesado de polímeros termoplásticos en extrusoras de doble husillo corrotantes
Alexander Knieper
La fusión inicial de polímeros termoplásticos por disipación de energía plástica no se comprende suficientemente y sigue siendo una laguna de conocimiento crucial en la descripción del proceso de la extrusora de doble husillo corrotante.
Se presenta una configuración de ensayo en la que se puede observar y registrar el transporte, la compresión y la deformación de gránulos de plástico en la sección transversal de la zona de plastificación de una extrusora de doble husillo. Se llevaron a cabo investigaciones sistemáticas con diferentes velocidades, temperaturas, polímeros termoplásticos, geometrías de pellets y niveles de llenado con el fin de demostrar su influencia en la fusión inicial debida a la disipación de energía plástica. La evaluación se llevó a cabo mediante grabaciones de alta velocidad y mediciones de par. Esta configuración permitió por primera vez obtener información sobre los parámetros que influyen significativamente en la fusión inicial por disipación de energía plástica de termoplásticos durante su procesamiento en extrusoras de doble husillo corrotantes.
Las investigaciones han demostrado que durante la disipación de energía plástica se suministra mucha energía al material en muy poco tiempo. Esto provoca un aumento local de la temperatura de aproximadamente 21 K en unas centésimas de segundo. El polímero, con sus propiedades mecánicas y termodinámicas, tiene una influencia decisiva en el aporte de energía. La cantidad de material que se deforma en la zona del fuelle depende principalmente del tamaño de los gránulos. A medida que aumentan la velocidad y la presión, se suministra más energía al material.
Comité de doctorado
Presidente: Prof. Dr. rer. nat. W. Reimers, Technische Universität Berlin Revisor: Prof. Dr.-Ing. M. H. Wagner, Technische Universität Berlin Revisor: Prof. Dr.-Ing. R. Weinlein, ikd, Darmstadt University of Applied Sciences
Día del debate científico: 20 de julio de 2018, Universidad Técnica de Berlín
Enlaces:
Caracterización de termoplásticos de alta temperatura en relación con la sinterización selectiva por láser y desarrollo de un grado de PPS sinterizable
Nico Baldassi
En este trabajo se demostró que es posible procesar un termoplástico de alta temperatura (PPS) mediante sinterizado láser con un sistema modificado.
El análisis y la optimización del PPS permitieron evaluar los métodos de caracterización. Se utilizó la poliamida 12 como referencia. Se demostró que los distintos métodos de medición para determinar la fluidez y la fluidez muestran la misma tendencia, pero no son directamente comparables entre sí. Cada método de medición es significativo en sí mismo, pero no puede transferirse. Las pruebas muestran que la fluidez depende en gran medida de la forma y el tamaño de las partículas. En particular, la distribución del tamaño de las partículas tiene una influencia significativa. Las fuerzas de adhesión entre partículas en el polvo también desempeñan un papel importante.
El control del proceso es el que más influye en la calidad de los componentes. Por lo tanto, la tecnología de planta disponible y utilizada desempeña un papel decisivo. En general, existe una gran necesidad de mejora en este aspecto, especialmente cuando se procesan polímeros alternativos. Esto se debe a la necesidad de un control más preciso del proceso cerca de la curva característica del polímero.
Comité de doctorado
Presidente: Prof. Dr. rer. nat. W. Reimers, Technische Universität Berlin Revisor: Prof. Dr.-Ing. M. H. Wagner, Technische Universität Berlin Revisor: Prof. Dr.-Ing. R. Weinlein, ikd, Darmstadt University of Applied Sciences
Día del debate científico: 14 de julio de 2016, Universidad Técnica de Berlín
Izquierda:
Procesado de termoplásticos largos reforzados con fibra de vidrio para aplicaciones de moldeo por inyección en la extrusora de rodillos planetarios
Thomas Birr
Esta tesis trata de la investigación de un método de procesamiento de termoplásticos reforzados con fibra larga utilizando una extrusora de rodillos planetarios como unidad de plastificación. El objetivo de este método es conseguir el menor daño posible de la fibra de vidrio durante la plastificación. Para conseguirlo, se investigan y optimizan las relaciones entre las configuraciones de la máquina, los parámetros del proceso y el daño resultante de la fibra, basándose en la distribución de la longitud de la fibra en el extruido. Sobre la base de estos resultados, se pueden extraer conclusiones sobre el modo de funcionamiento de la extrusora de rodillos planetarios, los mecanismos que se producen y los procesos de flujo, que apoyan la comprensión general de este tipo de máquina hasta ahora poco descrito.
Las extrusoras de rodillos planetarios están concebidas principalmente para aplicaciones de compounding y procesamiento y, en principio, no son adecuadas para la producción directa de componentes moldeados por inyección. Para que esto fuera posible, la extrusora se amplió a una mezcladora de moldeo por inyección mediante un sistema de almacenamiento de masa fundida. En esta tesis se analiza el diseño y las pruebas de este sistema, especialmente concebido para el procesamiento de fibras largas, y se examina todo el procedimiento de procesamiento.
A fin de garantizar la comparabilidad con el moldeo por inyección convencional, las pruebas se llevaron a cabo utilizando granulados de PP-LGF pultrusionados, un grupo de materiales habitual en la producción industrial. Se comprobó que con este tipo de materiales puede conseguirse un proceso de fusión con escaso daño de las fibras utilizando la extrusora de rodillos planetarios. La experiencia adquirida también sugiere que un método de procesamiento directo también es posible y podría tener más efectos positivos en términos de procesamiento respetuoso con la fibra.
Comité de doctorado
Presidente: Prof. Dr. rer. nat. W. Reimers, Technische Universität Berlin Revisor: Prof. Dr.-Ing. M. H. Wagner, Technische Universität Berlin Revisor: Prof. Dr.-Ing. R. Weinlein, ikd, Darmstadt University of Applied Sciences
Día del debate científico: 07.07.2015, Universidad Técnica de Berlín
Enlaces:
Influencia de la tecnología de proceso de una extrusora de rodillos planetarios en la conductividad eléctrica de poliolefinas rellenas de negro de humo
Thomas Taufertshöfer
Para que los plásticos sean conductores de la electricidad, se mezclan cargas en la matriz polimérica durante la composición. Si se acepta el color negro, el negro de humo es el material elegido porque es el más fácil de procesar y el más económico. El proceso de mezcla es el mayor reto para el mezclador. Para obtener un buen compuesto, el negro de humo debe distribuirse homogéneamente en la matriz polimérica y conservar su estructura, sensible al cizallamiento. Si es posible conservar la estructura del negro de humo, se puede conseguir una red continua y eléctricamente conductora de negro de humo con un bajo contenido de relleno. Este trabajo investiga la influencia de la tecnología de proceso de una extrusora de rodillos planetarios (PWE) en la conductividad eléctrica de las poliolefinas rellenas de negro de humo. Los compuestos basados en plásticos semicristalinos se producen en diferentes condiciones de procesamiento y con diferentes contenidos de negro de humo. La conductividad eléctrica se determina en probetas moldeadas por inyección y prensadas. Además de las propiedades eléctricas, también se investigan las propiedades morfológicas y mecánicas. En el proceso de moldeo por inyección, la dosificación directa en la masa fundida conduce a la conductividad eléctrica más alta, mientras que el proceso de prensado de placas conduce a la más baja. Otra conclusión de este trabajo es que la conductividad eléctrica está menos influida por la tecnología de proceso de la extrusora de rodillos planetarios que por el tipo de negro de humo, el contenido de negro de humo y el método de procesamiento. Al analizar las propiedades mecánicas de las probetas de ensayo, se encontró, como era de esperar, que la resistencia al impacto entallado y los valores de elongación disminuyen con el aumento del contenido de negro de humo, mientras que los valores característicos relevantes para la resistencia, como el módulo de tracción y la tensión de rotura, mejoran.
Comité de doctorado
Presidente: Prof. Dr. rer. nat. W. Reimers, Technische Universität Berlin Revisor: Prof. Dr.-Ing. M. H. Wagner, Technische Universität Berlin Revisor: Prof. Dr.-Ing. R. Weinlein, ikd, Darmstadt University of Applied Sciences
Día del debate científico: 10 de diciembre de 2013, Universidad Técnica de Berlín
Enlaces:
Disertación en el repositorio de la TU de Berlín.
Desarrollo de una tecnología de anillo dispersor ajustable para extrusoras de rodillos planetarios
Marcus Greger
En este trabajo se desarrollan, evalúan y someten a pruebas nuevos anillos dispersores ajustables para su uso en una extrusora de rodillos planetarios. El desarrollo se centra en la rápida ajustabilidad de los anchos de separación a la base del eje y el ahorro de tiempo y la reducción de costes asociados al cambiar los requisitos de composición en comparación con los anillos de dispersión no ajustables utilizados anteriormente en una extrusora de laboratorio. Además de la ajustabilidad, también se pretende mejorar la dispersión de los polvos coloreados que tienden a aglomerarse en los polímeros fundidos. La capacidad de carga y las posibilidades de posicionamiento del anillo de dispersión se consideran criterios de evaluación mecánica. La energía de accionamiento específica se utiliza como medida de funcionalidad comparable entre anillos de dispersión ajustables y no ajustables. El desarrollo de los anillos de dispersión con respecto a una distribución homogénea de los aditivos se evalúa, por un lado, mediante microscopía y el análisis de imagen asociado de la distribución de partículas y, por otro, mediante la medición del color del granulado utilizando diferencias de color. El análisis de las diferencias de color desempeña un papel fundamental en esta parte del análisis. El polvo de color utilizado es Cu-ftalocianina, que es difícil de mezclar en las extrusoras convencionales de doble husillo.
Comité de doctorado
Presidente: Prof. Dr. rer. nat. W. Reimers, Technische Universität Berlin Revisor: Prof. Dr.-Ing. M. H. Wagner, Technische Universität Berlin Revisor: Prof. Dr.-Ing. R. Weinlein, ikd, Darmstadt University of Applied Sciences
Día del debate científico: 01.11.2011, Universidad Técnica de Berlín
Izquierda: